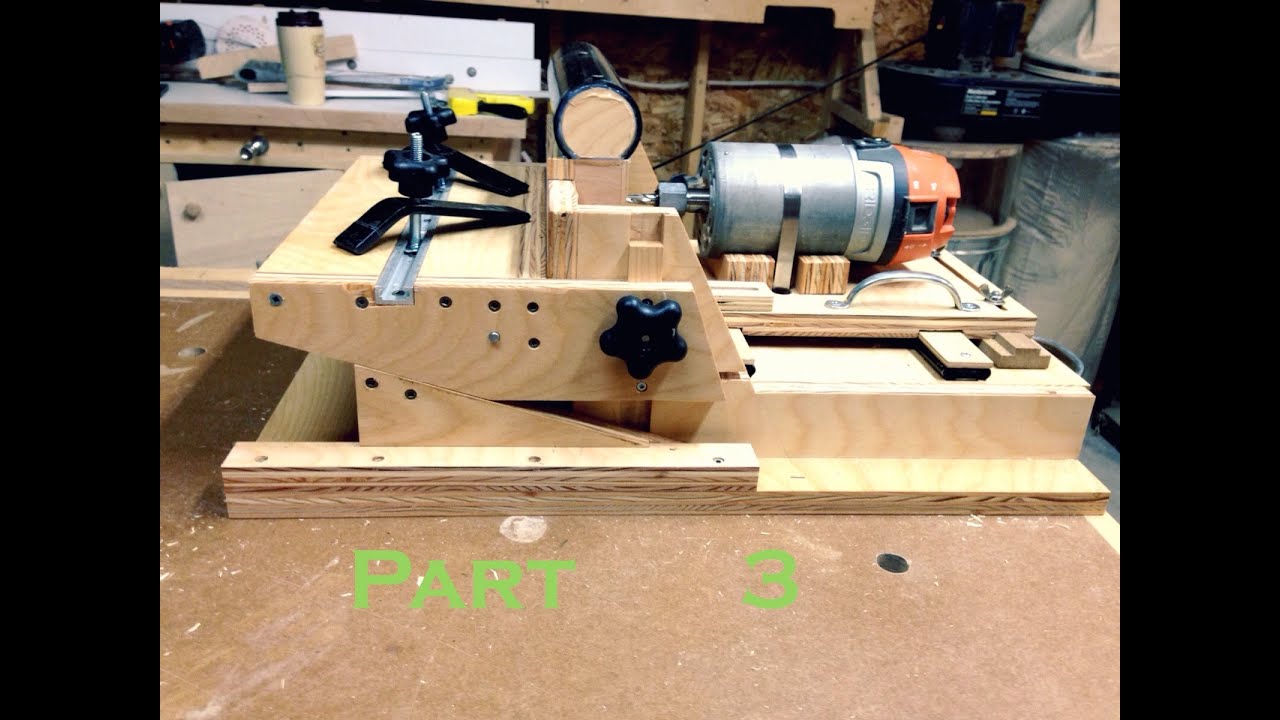
7901 Industry Drive North Little Rock, AR 72117: Phone (800) 787-6747 Fax (501) 945-0312 Mail info@tech-mark.com. The Zip Slot has a vacuum attachment. That is a 2 1/2 opening. My old Sears vacuum easily slips into the jig, but the suction holes to the stock are small causing the vacuum to work a lot harder than it should. The vacuum heated up during a long session of mortise cutting so I had to shut it off while changing stock.
Slot Mortiser Part 18
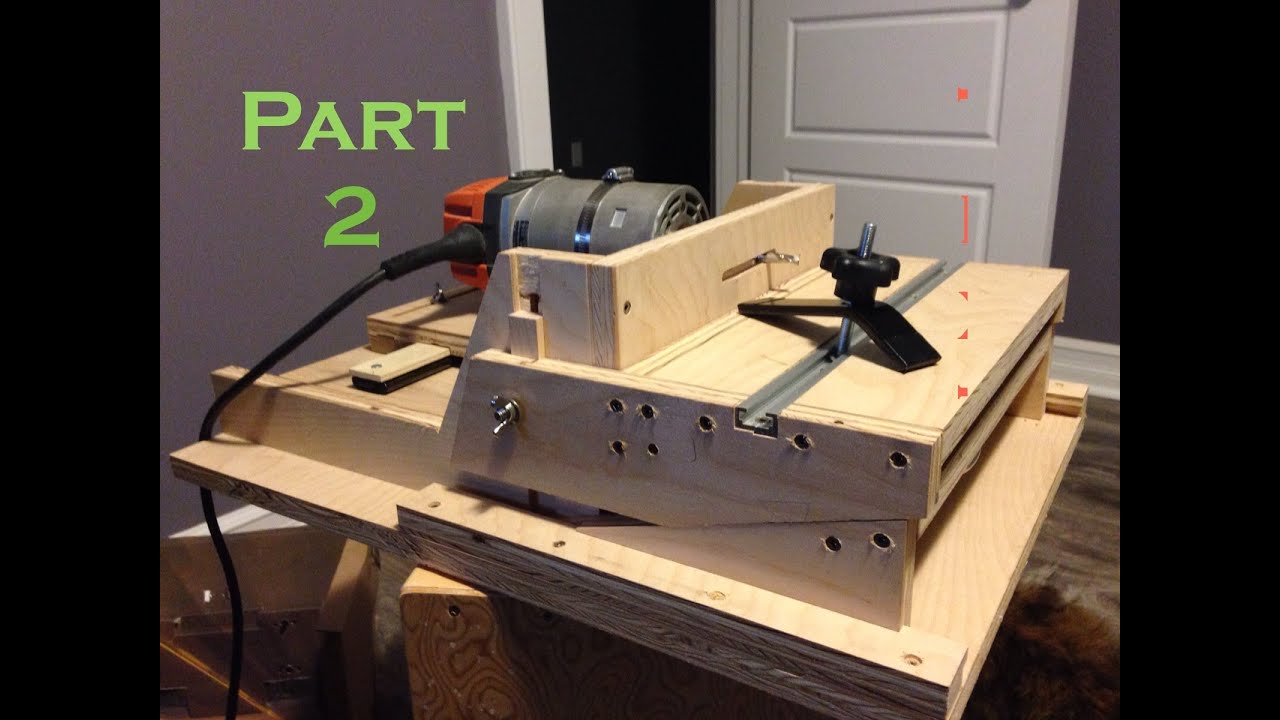
7901 Industry Drive North Little Rock, AR 72117: Phone (800) 787-6747 Fax (501) 945-0312 Mail info@tech-mark.com. The Zip Slot has a vacuum attachment. That is a 2 1/2 opening. My old Sears vacuum easily slips into the jig, but the suction holes to the stock are small causing the vacuum to work a lot harder than it should. The vacuum heated up during a long session of mortise cutting so I had to shut it off while changing stock.
Slot Mortiser Part 18
The Thien Mortise Jig Last weekend (early April 2011), I was working on a walnut medicine cabinet using some beautiful straight-grained walnut I had found the previous weekend at my hardwood supplier. I was assembling the face frame with pocket screws when I heard a c-r-A-C-K. The 2nd to the last screw cracked the stile going in. Badly. It would be easier to start over than to fix the frame. I had enough wood left to make one more frame, so I used dowels to assemble it. I like dowels enough, but positioning the jig can be tedious (IMHO). I know others disagree, but having side to side play in the joint and then being able to align things during glue up, like a biscuit jointer or a Domino with an oversize (wide) cut takes a lot of the worry out of getting things perfect while cutting the joints. So a Domino would be ideal. But I didn't have one. The cracked walnut stile had me convinced I needed one, so I actually posted a wanted ad for a used Domino. I couldn't justify the $850 a new one costs. I've seen used ones go for $650. Still a lot of money to spend, but it seemed like it would allow me to join narrow pieces of stock in a fast and efficient manner. I figured that while watching for a used Domino, I'd investigate mortising jigs. I'd been thinking about making a mortising jig to use with my little DeWalt DW611 plunger. It has great dust collection. It plunges nicely. It seems like it would be the perfect candidate for a compact mortising jig. Many of the jig plans out there (Shop Notes, etc.) are for larger jigs. I wanted something smaller. Something I could 'take to the wood,' if desired. Something I could use at the bench (clamped) like a full-size jig, but also something that I could clamp to a large workpiece out of the driveway. I wanted flexibility! I also decided that using multiple floating tenons (like using multiple biscuits or multiple dowels or multiple Dominos) was preferred to adjusting the size of the mortise to the size of the stock. So for a face frame, I'd use a single 1' x 1-1/2' x 1/4' floating tenon. For attaching an apron to a leg, I might use two or four. I can produce my own 'one-size-fits-all' tenons in advance and always have plenty on hand.
I routed a relief in the bottom of the template, hoping the dust could escape. That didn't help. So I enlarged the slot and used a larger bushing. Still no good. Looking at the bottom of the router, I decided my next attack would be to remove two of the screws for the plastic sub-base, and use longer screws with plastic spacers to create guides that would ride in 3/8' wide slots in a new template. Well, this worked even better than expected. With the bushing out of the picture, dust was properly evacuated from the mortise. And the 3/8' spacers I found at my local hardware store fit in a 3/8' wide slot cut by a router bit PERFECTLY. The router moves like it is on rails. The width of the mortise (1-1/8') is controlled by the center (non-wasted) part of the slot. As the 3/8' spacers I've attached to the bottom of the router reach the end of their slots, they stop the router from moving any further. For smaller workpieces, I prefer to use my template on a larger fence I clamp in my workbench vise. But I've also made a smaller fence that allows me to clamp the template directly to a larger workpiece (a table stretcher, for example). The edge-to-mortise distance is controlled by two screws (the black ones) that you see on top of the jig. I used knock-down furniture screws because they have large yet thin heads. They thread into cross-dowels in the fences. I purchased all the hardware at my local Ace Hardware. I was surprised when I assembled the first joint and saw just how nicely it fit together. There was just enough side-to-side play to align edges nicely during glue-ups, and yet the faces of the first and subsequent test pieces have been perfectly flush. I normally impress myself, but not THIS much. This design should be adaptable to many different types of routers. Anything that has holes for mounting a sub-base. I especially like the DW611, as it is nice and compact and easy to maneuver.
--Phil This page has been viewed times. |
Slot Mortiser Part 1 Diagram
I'm very much a fan of mortise and tenon joinery. The classic North American power tool for making mortises is a hollow chisel mortiser. I have been a little dismissive of hollow chisel mortising all along, but I thought I should explore the technique a bit more. This article is about my experiments at building such a mortiser out of mostly wood.My plan was to cobble together a proof of concept machine, and then, based on that experience, design a more robust and elegant second machine, similar to what I did with the Pantorouter I don't think I will build a second machine at this point though, so I figured I might as well tell you about my proof of concept machine and why I decided not to build a machine. About twenty years ago, my dad bought a hollow chisel mortiser drill press kit. He tried it out once, decided it was too slow, and then never used it again. He offered it to me years ago, and on my visit last Christmas, I finally took him up on the offer. I figured this kit would be a good starting point for building a hollow chisel mortiser. The kit consists of a bracket (top left in image) that attaches to the drill press quill and reaches around the chuck to hold the chisel, four chisels (1/4', 5/16', 3/8' and 1/2'), and this funny bracket (top right) to attach to a fence on the drill press table to hold down the stock. You can get this style of kit for as little as $40 (without the chisels), so I figured a kit like this could be the basis of a cheap hollow chisel mortising machine design. I had to cut parts off the bracket to allow the hand drill to fit inside it. This bracket is meant to fit around a 2 5/8' diameter quill on the drill press. It didn't fit on my drill press, so I couldn't even try it out before I cut it open. I also drilled some extra holes in the bracket to screw it down on the plywood. Cast iron is remarkably easy to drill! The idea was to mount this part on a piece of plywood. I cut a slot in the plywood so that part of the casting could fit into it. A lot of force is required when hollow chisel mortising, so I figured the best way to support the casting is by letting it push right up against the plywood base itself. Another block holds the front of the bracket. Between the two of them, I should have pretty good support. I also added several blocks to mount the drill. The drill I used has part of the plstic housing cylindriecal near the front, which makes it relatively easy to mount. I used some very cheap packing crate plywood. This was meant to be my proof of concept machine, so I didn't want to use up any of the good birch plywood. The plywood that holds my cast iron bracket and hand drill slides up and down on dovetails on either sides of it. The dovetail rails are screwed to the side of the plywood. This would allow me to adjust the fit of the dovetail. Basically, cut small slivers off the plywood until the dovetail becomes tight. If I cut too much off, I can always add shims to make it looser. The other half of the dovetail is just the edge of the plywood. Not ideal. If I was building a permanent machine, I might add a strip of wood to glide on. Or maybe put a layer of UHMW tape against the edge of the wood. As it is, I put two coats of varnish on the plywood edge to make it glide a little easier. And here's my proof of concept machine making the first mortises. The basic frame of the machine is actually the stand that I used for my joint strength tests, with the mortising mechanism just clamped to the front of it. For a final machine, I would have made a frame more optimized for this application. It can take a lot of force to ram that chisel into the wood, so I added a piece of 2x2 (38 x 38 mm) as a lever. The lever pivots on two 3/8' (10 mm) bolts. The vertical piece on the right is only screwed loosely to the plywood piece with the drill on it to allow it to pivot. (a little inelegant, but good enough to try the concept). Two springs counteract gravity so that the mechanism rests in the 'up' position when I let go of the handle. The two bar clamps are there to hold the mechanism to my stand. The clamps don't have to take up the vertical forces - there's a metal ledge that's part of my stand that the mechanism hooks on to, although you can't really see that in the photo. Here's the chiseling head of the machine. I added two wooden hooks to hold the piece down while I pull the chisel up. It can take a lot of force to pull the chisel back out of the wood, especially after the first plunge. Cheap hollow chisel mortisers tend to use a similar mechanism to hold the stock down. It would have been good to use the funny bracket for holding the stock to a fence that came with the mortising kit, but the bracket would have interfered with how I mounted the part that holds the chisel. On better hollow chisel mortisers, there's a clamp for holding the stock. But this requires the mortiser have a table that can move side to side. On cheap mortisers one just moves the stock side-to-side. That previous photo was a close up of Jacques Jodoin's General International hollow chisel mortiser. When I revisited Jacques to check out his Ryobi WDP, I also took the opportunity to play with his hollow chisel mortiser as well. Now back to my proof of concept jury-rigged contraption. The mortiser kit had a screw knob for locking the chisels in the mortiser. But with my wooden block clamped around the front of the bracket, I had to find a longer bolt. If this were a proper machine, I'd make a wooden knob for this bolt. But seeing that it was just an experiment, I didn't bother. I also didn't have much of a depth stop. I started by just putting a C-clamp on my dovetail to limit how far it could come down. But hollow chisel mortisers involve so much force, I found my clamp slipping without even noticing that I was pushing it. So I clamped a block of wood to the dovetail. The block of wood gets pushed up against my bracket that holds the wood, so it can't slip. Inelegant, but works well enough to try it out. Side profile view. I was lucky that my drill has a bit of a hook on the back to help push it. I made a wooden block that fits exactly against the hook, and i screwed it onto the plywood with four screws. That block will take up the force on the drill. It's not overly critical, because most of the force goes to the hollow chisel, not the drill bit. Making lots of mortises to test. The drill I was using is a 0-3000 RPM drill, and I set the speed to just a few hundred RPM. There's no speed regulation at all, and with the drill only having a single stage gear reduction, it doesn't provide for very steady speed at low speeds and high torque. With the 3/8' chisel, it slows down a fair bit when mortising. The 3/8' chisel is the second largest I have. The largest is 1/2', but I don't think my proof of concept machine is robust enough to really try that one, and I don't think that hand drill would be up to the job either. The other problem with the drill I'm using is that it's a hammer drill. The hammer function can of course be turned off. But even with it off, the drill chuck will move back by about two millimeters when pushed. This means I need to let the drill stick that much further out of the front of the chisel to allow the bit and chuck movement when mortising. I used that drill because it doesn't have a keyless chuck, and because it has the nice cylindrical part to mount on the front. It was a really cheap drill - it only cost me $20. But it's also the kind of quality you get for $20! Other than only having a single stage gear reduction and a chuck that moves back, it would have been perfect for the job. Once I got the hang of using the machine and made a few good mortises, I cut some of them open on the bandsaw to see how they looked on the inside. What I didn't like is that the bottom of the mortise isn't clean. This is because the drill bit has to protrude forward of the chisel by quite a bit. So if I made my mortises with a hollow chisel mortiser, I'd have to make the tenon not protrude to the full depth of the mortise. That, or clean up the bottom of the mortise with a chisel. But the whole idea of experimenting with hollow chisel mortising was to get square holes so I could just put square tenons in them without having to fuss. If I have to clean it up with a chisel, I might as well start with a slot mortise and square up the ends, round the tenons with a hand file, or make round ended tenons to begin with. By comparison, here's a cut open mortise that was done on Jacques Jodoin's hollow chisel mortiser (see picture earlier). Not much different on the bottom. The walls of his mortise look better, but maybe his chisel was sharper. I also noticed the left and right edges on this mortise weren't entirely vertical (compared to the pencil lines I added with a square). The problem is that the chisel really pulls into the wood on either side, especially if the chisel is only engaging the wood on one side. My own mortising contraption did worse than Jacques's in this regard. So I was really starting to question the point of hollow chisel mortises. Slot mortises have the annoyances of round ends, but hollow chisel mortises have plenty of issues as well. I really should use a more solid, lower RPM drill with the mortiser. So I went shopping for something more suitable, preferably in the $50 price range, as opposed to $20 price range. It turns out, there are quite a lot of drills that are cylindrical on the front, have a nice hook on the back, and keyed chucks. Problem is, nearly every drill that has those properties is a hammer drill, with a chuck that moves back a little when you push on it, even with the hammer function turned off. There was one nice DeWalt drill that wasn't a hammer drill and would have been perfect, but that drill cost $150. At that price, it would make more sense to just buy a low end mortiser for about $200. Even if I could build a better mortiser than a low end mortiser, it would make more sense to start with the low end mortiser as raw material! So that really put me off building a mortiser. I'd end up spending about as much as it costs to buy a cheap one. Mortising (even on a proper hollow chisel mortiser) is slower than slot mortising. The resulting mortise is less accurate because of all the force involved, and there's the problem with having to make shorter tenons or clean up the bottom of it. So I conclude that it makes more sense to build a slot mortiser than a hollow chisel mortiser. By the time I'd have it done, the hollow chisel mortiser would be more work than the slot mortiser or the pantorouter A more practical application of what I came up with might be to use that same mechanism, without the hollow chisel part, to turn a hand drill into a drill press. But then you have to weigh off the cost of a cheap drill press to that of a good hand drill, and there probably aren't any savings there either. Having said all that, If you are not up for building your own machines, low end hollow chisel mortisers are surprisingly cheap - so if you are just starting out and want a machine for making mortises, it would be quite expedient to buy one of these cheap hollow chisel mortisers and use that until you have the money or time to buy or build something better. The other nice thing about hollow chisel mortisers is that they don't make much dust, and that they are quiet; Although my contraption, with the cheap hand drill strapped on, wasn't that quiet. For my own work, I'll stick to slot mortising. More on Mortise and tenon joinery See also: Back to my woodworking website. |